The spiral paper tube winding machine is an industrial equipment specially used for making paperboard tubes and cores. The working principle of this machine is to spirally wind layers of kraft paper or paperboard around a mandrel of 2-8 inches or even larger to form the desired tube diameter.
Adhesives are used during the winding process to fix the layers and form a strong bond. The machine may contain cutting, bonding and finishing processes to produce customized tubes of various sizes and specifications. Paper tube making machines are indispensable in industries such as packaging, textiles and construction, which require strong cylindrical structures for packaging, winding materials or structural support.
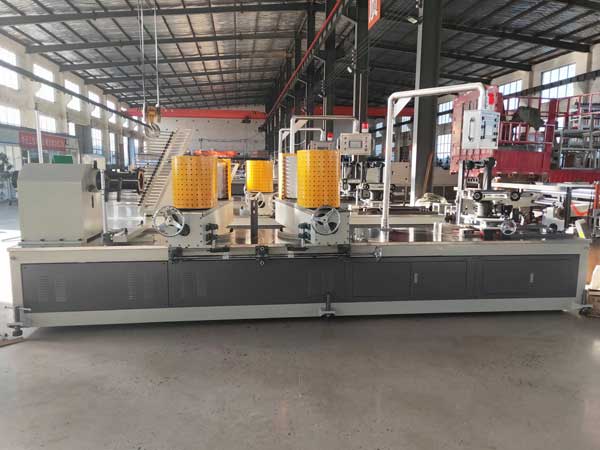
Once you have determined that you need a new spiral paper tube winding machine, a very important question will arise: which brand to trust?
In order to answer this question, you need to work hard to learn more about the spiral paper tube winding machine, such as working basis, characteristics, parameters, etc.
Watch the video of the paper tube machine on Youtube to understand its basic working process.
Spiral Paper Tube Winding Machine Performance
For the spiral paper tube winding machine, first confirm what length, thickness, inner diameter you need to produce, and where to use it.
Because these parameters are particularly important for determining the appropriate model.
Number of papers:3-25 layers
Inner diameter of paper tube:40-500(mm)
Thickness of paper tube: 2-15(mm)
Tube rolling speed:0-25(m/min)
Cutting method:CNC Automatic Tracking for Cutting
Fixed method of core mold: Flange tightening
Control method:Frequency control
Input voltage:380V/220V
The winding of the spiral paper tube winding machine is driven by the motor and the gearbox, so you must pay attention to the brand and power of the motor, as well as the speed ratio of the gearbox. With the increase of motor power and gearbox speed ratio, the winding force of the kraft paper tube is greater, the kraft paper tube is wound tighter, the tube quality is better, and it is more popular with end customers. However, if the speed ratio is too large, the paper rolling speed is relatively slow and the production efficiency is reduced. Therefore, it is necessary to strike a balance between quality and speed and choose the appropriate motor power and gearbox speed ratio.
Spiral Paper Tube Winding Machine Process Flow:
1. Large roll paper slitting: slitting large roll base paper into suitable production width for subsequent process.
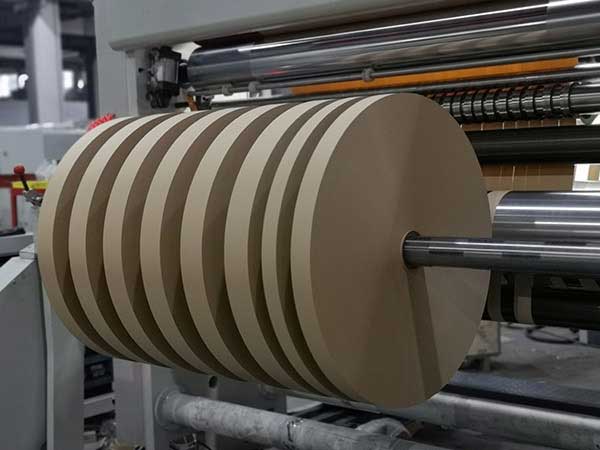
2. Glue adjustment: according to the specifications and requirements of paper tube, mix appropriate glue to ensure bonding strength and quality.
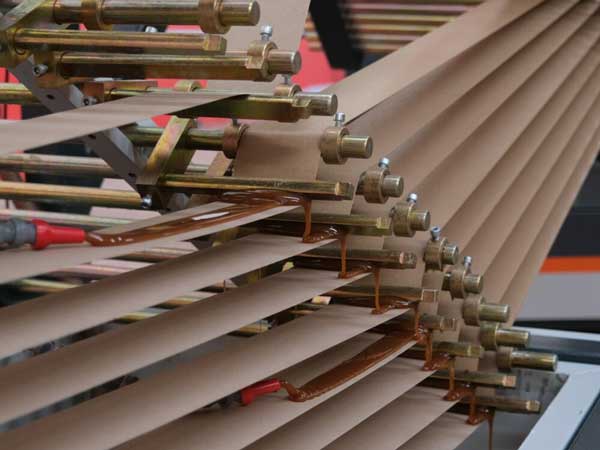
3. Tube rolling: the slit paper strip is rolled into a tube through spiral paper tube winding machine, and glue is applied at the same time to ensure the bonding between paper layers.
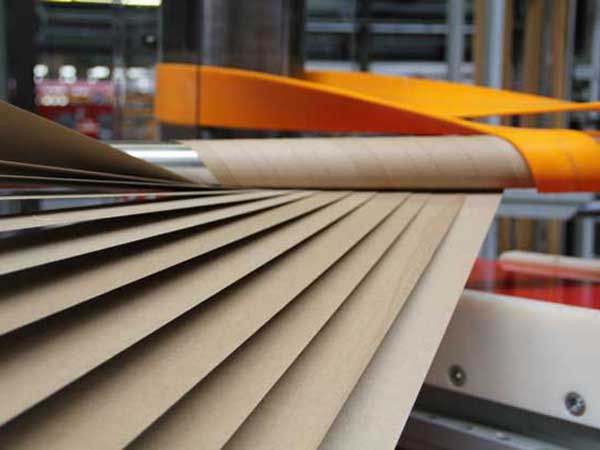
4. Tube cutting: according to the required length, the rolled paper tube is cut into standard length tubes.
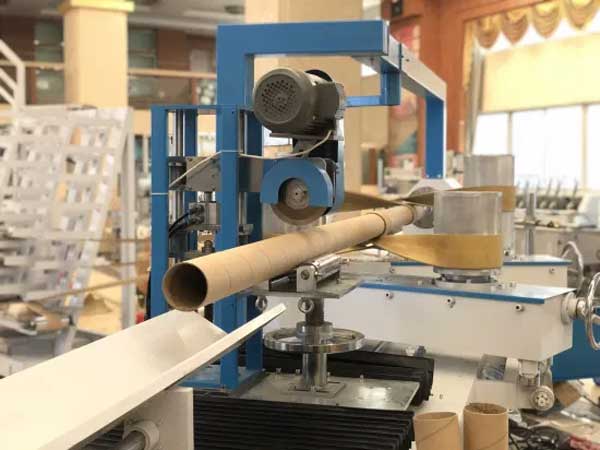
5. Tube drying: place the freshly cut tube in the drying area or use drying equipment to remove excess moisture and improve the strength of the tube.
6. Precision cutting of tubes: place the freshly cut tube in the drying area or use drying equipment to remove excess moisture and improve the strength of the tube.
7. Polishing: polish the surface of the paper tube to make it smoother and more beautiful.
8. Packaging: package the finished paper tube for easy transportation and storage.
Spiral Paper Tube Winding Machine Uses:
1. High-grade seamless paper tube
The surface of the paper tube is seamless, ultra-smooth, dust-free, environmentally friendly, cost-effective, and easy to process again. It is especially suitable for high-speed winding of ultra-thin plastic film, metal foil, paper, and EVA film.
2. High-strength, high-smooth paper tube
The surface is seamless, wavy, high flatness, high strength, high straightness, high roundness, high surface hardness, moisture-proof, and dust-free. It is suitable for high-speed winding of thin materials such as high-grade plastic film and metal foil.
3. Large-diameter paper tube
It is strong and durable, suitable for stainless steel, color steel plate, aluminum foil, copper strip, cardboard, construction and other industries, with large volume, strong load-bearing capacity, low cost, energy saving, and environmental protection.
4. High-strength tube
It has high compressive strength and stable surface gap. It is widely used in papermaking, film, and other large-load and high-speed winding industries with high cost-effectiveness.
5. Thick tube
The thickness of the paper tube is generally 25.4mm, and the thickest can reach 75mm, which can meet the high-speed winding of materials such as glass fiber and non-woven fabrics.
It is also commonly used in industries such as construction and decoration.
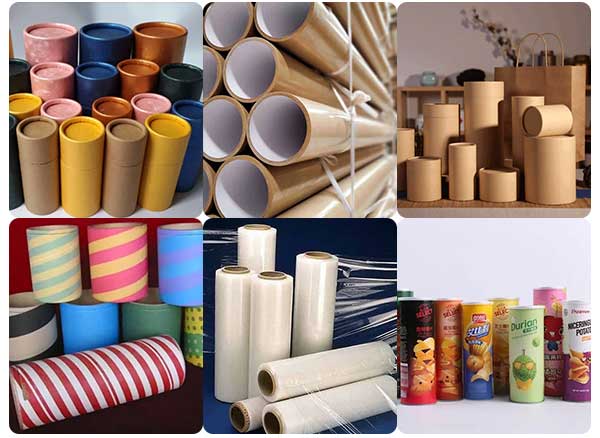
Why Choose Us?
There are many manufacturers of spiral paper tube winding machine. However, choosing the right one may be a bit difficult, and here are some factors worth considering. We have a professional installation and after-sales team to provide you with high-quality technical support and perfect after-sales service.
The factory covers an area of 60,000 square meters. After nearly 30 years of development, the company currently has 178 employees and 23 engineering and technical personnel. If you have spiral paper tube winding machine needs, please contact us immediately!